CNC Turning Parts Manufacturer
The five-axis machining center is also called a five-axis machining center. It is a high-tech, high-precision machining center specially used for processing complex curved surfaces. This machining center system is important for a country’s aviation, aerospace, military, scientific research, and precision. Industries such as equipment and high-precision medical equipment have a decisive influence. The five-axis linkage CNC machining center system is the only means to solve the processing of impellers, blades, marine propellers, heavy generator rotors, steam turbine rotors, large diesel engine crankshafts, and so on.
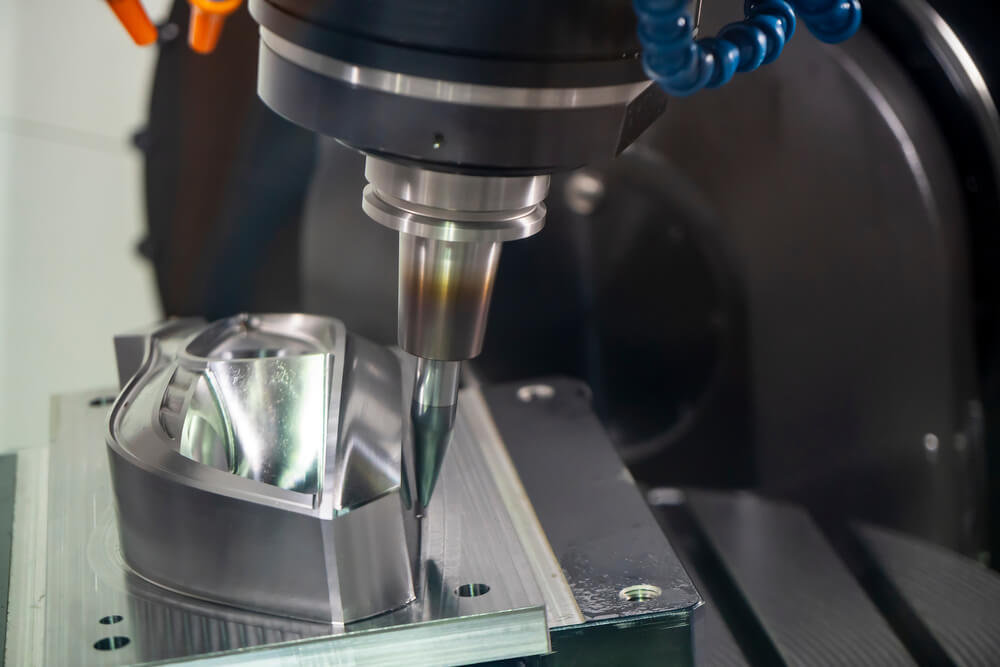
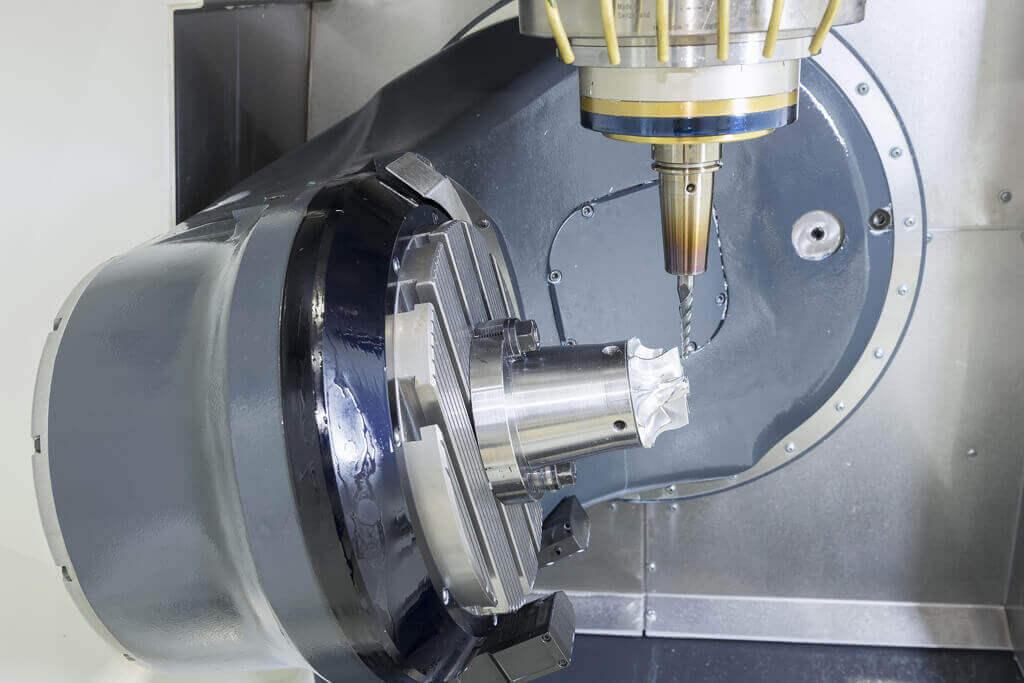
The five-axis machining center has the characteristics of high efficiency and high precision, and complex machining can be completed in one clamping of the workpiece. It can be adapted to the processing of modern molds such as auto parts and aircraft structural parts. There is a big difference between a five-axis machining center and a five-sided machining center. Many people don't know this and mistake the pentahedral machining center as a five-axis machining center. The five-axis machining center has five axes x, y, z, a, and c. The xyz and ac axes form a five-axis linkage processing. It is good at space surface processing, special-shaped processing, hollow processing, punching, oblique hole, bevel cutting, etc. The "pentahedral machining center" is similar to a three-axis machining center, except that it can do five faces at the same time, but it cannot do special-shaped machining, beveled holes, cut bevels, etc.
The commonly used simulation software for five-axis machining centers is called PITAGORA. What does this software do?
Usually, when we operate the five-axis equipment for processing, we need to program or make drawings in advance. Due to manual operation problems, it may or cause program errors, which will inevitably lead to an impact event, which may damage the equipment. PITAGORA software is used to simulate actual processing. It can predict whether there is an error in advance, so as to reduce the accident rate to a minimum and ensure the safety of the equipment!
In Summary,
The five-axis machining center is not only used in civil industries, such as wood mold manufacturing, bathroom trimming, automotive interior parts processing, foam mold processing, European style home furnishings, solid wood chairs, etc., but also widely used in aviation, aerospace, military, scientific research, precision Equipment, high-precision medical equipment and other industries. The five-axis machining center is a high-tech method that makes the impossible possible. All spatial curved surfaces and special-shaped machining can be completed. It can not only complete the task of mechanized processing of complex workpieces, but also quickly improve processing efficiency and shorten processing procedures.
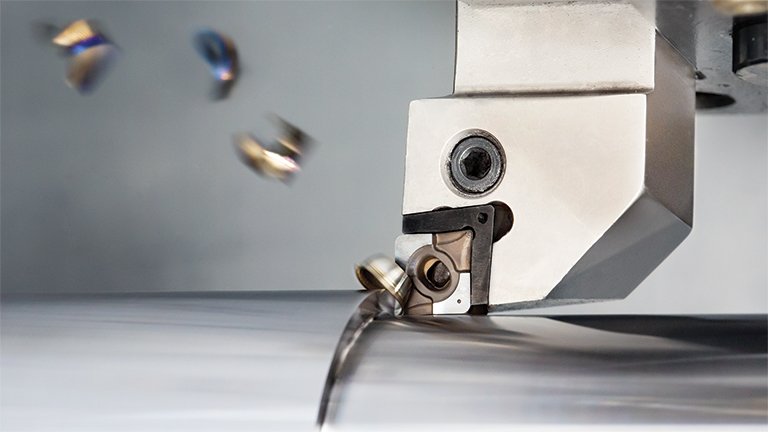
Send your message to us:
-
Aluminum CNC Machining Parts
-
Aluminum Sheet Metal Fabrication
-
Auto Parts Machining
-
Axis High Precision CNC Machining Parts
-
CNC Machined Components
-
CNC Machining Aluminum Parts
-
CNC Machining Metal Parts
-
CNC Machining Service Turning Parts
-
CNC Milling Machine Components
-
Custom Aerospace Sheet Metal Parts