CNC Machining Definition
Numerical control machining refers to a process method for processing parts on a CNC machine tool. The process regulations of CNC machine tool processing and traditional machine tool processing are generally consistent, but significant changes have also taken place. A machining method that uses digital information to control the displacement of parts and tools. It is an effective way to solve the problems of variable parts, small batches, complex shapes, and high precision, and to achieve high-efficiency and automated processing.
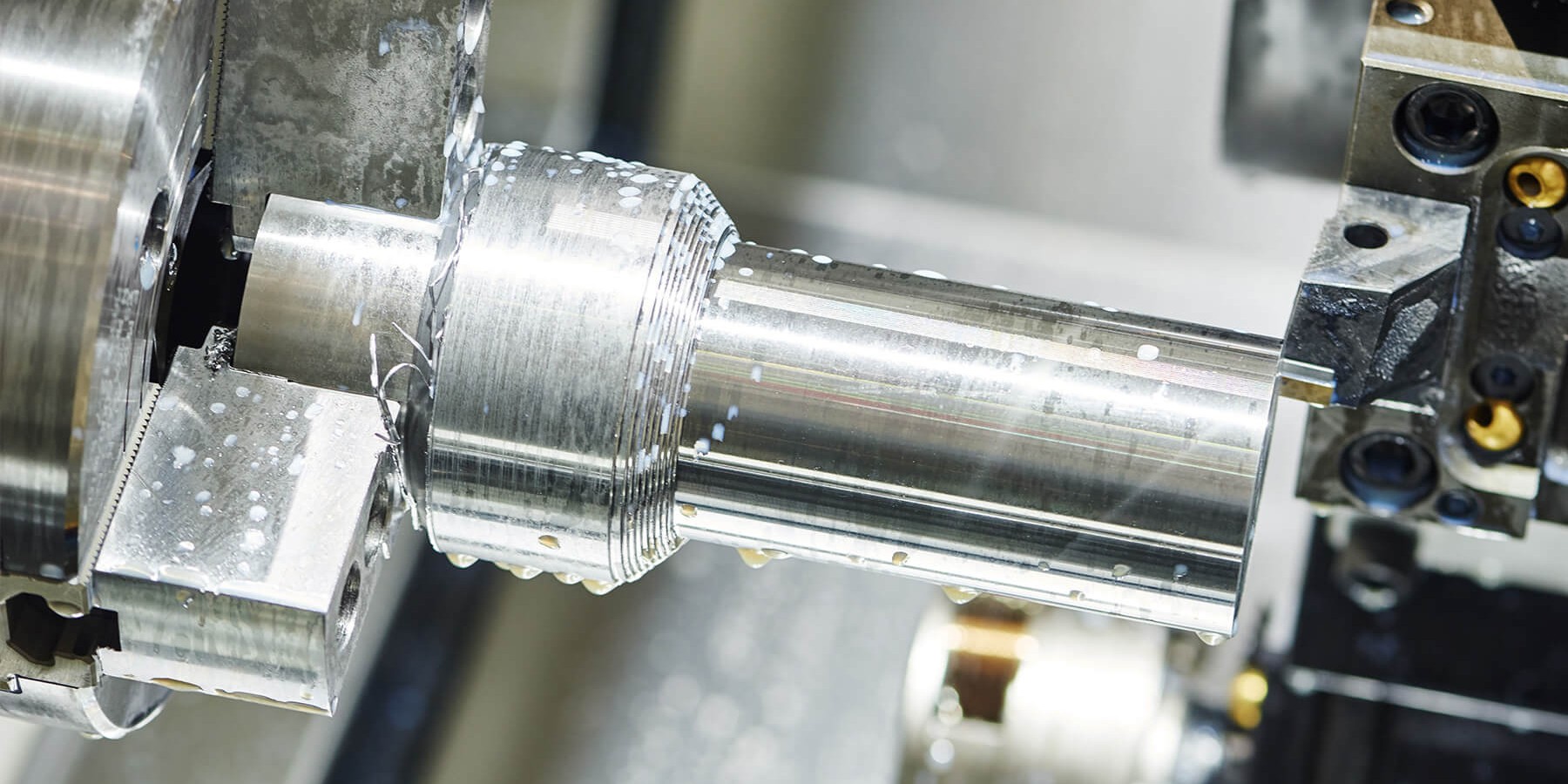
Numerical control technology originated from the needs of the aviation industry. In the late 1940s, a helicopter company in the United States put forward the initial idea of a CNC machine tool. In 1952, the Massachusetts Institute of Technology developed a three-axis CNC milling machine. This kind of CNC milling machine has been used for processing aircraft parts in the mid-1950s. In the 1960s, numerical control systems and programming work became increasingly mature and perfect. CNC machine tools have been used in various industrial sectors, but the aerospace industry has always been the largest user of CNC machine tools. Some large aviation factories are equipped with hundreds of CNC machine tools, of which cutting machines are the main ones. CNC machining parts include integral wall panels, beams, skins, bulkheads, propellers, and aero engine casings, shafts, disks, blades, and special cavity surfaces of liquid rocket engine combustion chambers.
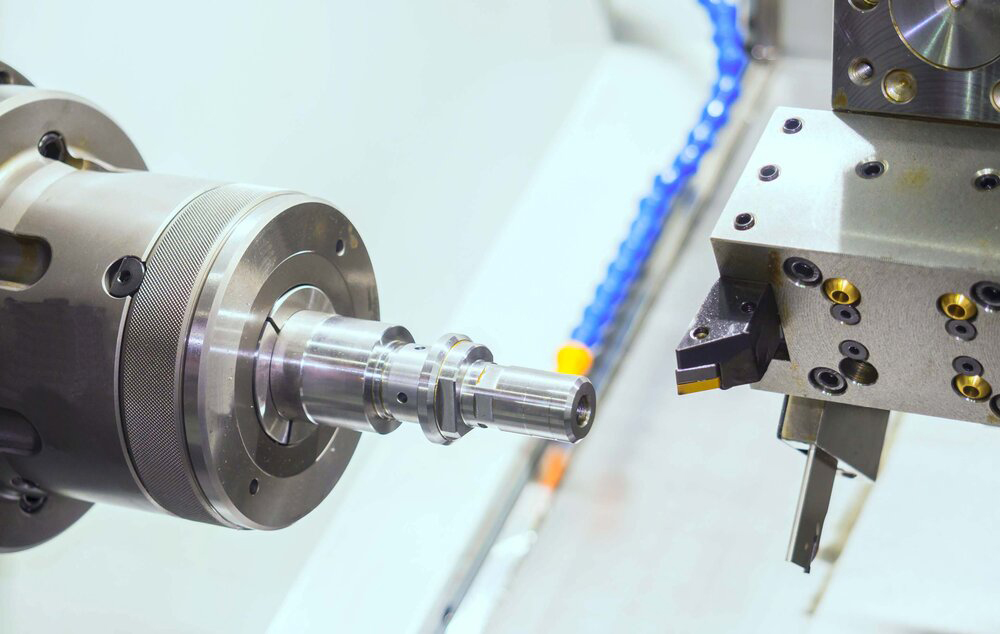
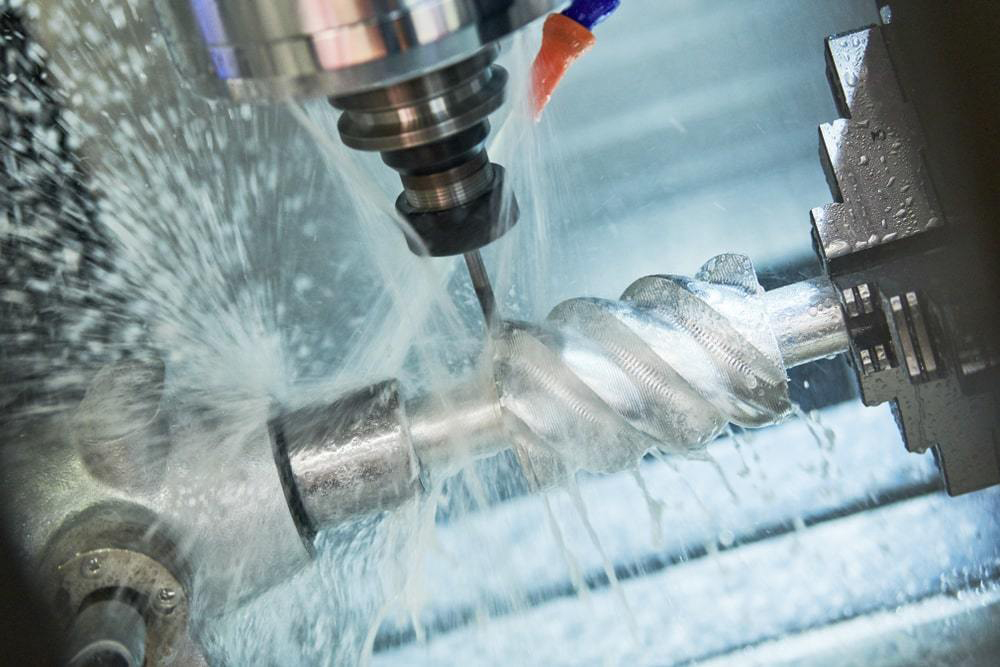
The initial stage of the development of CNC machine tools is based on continuous trajectory CNC machine tools. Continuous trajectory control is also called contour control, which requires the tool to move on a prescribed trajectory relative to the part. Later, we will vigorously develop point-control CNC machine tools. Point control means that the tool moves from one point to another, as long as it can reach the target accurately at the end, regardless of the moving route.
CNC machine tools select aircraft parts with complex profiles as the processing objects from the very beginning, which is the key to solving the difficulty of ordinary processing methods. The biggest feature of CNC machining is the use of punched tape (or tape) to control the machine tool for automatic processing. Because airplanes, rockets, and engine parts have different characteristics: airplanes and rockets have zero parts, large component sizes, and complex shapes; engine zero, small component sizes, and high precision.
Therefore, the CNC machine tools selected by the aircraft and rocket manufacturing departments and the engine manufacturing departments are different. In aircraft and rocket manufacturing, large-scale CNC milling machines with continuous control are mainly used, while in engine manufacturing, both continuous-control CNC machine tools and point-control CNC machine tools (such as CNC drilling machines, CNC boring machines, machining centers, etc.) are used.
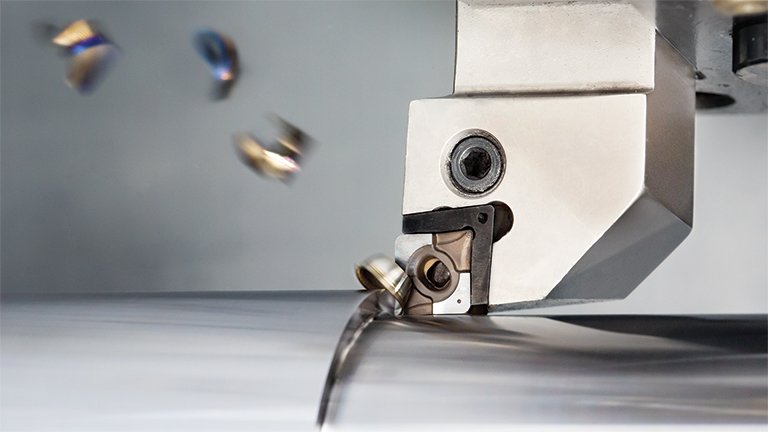
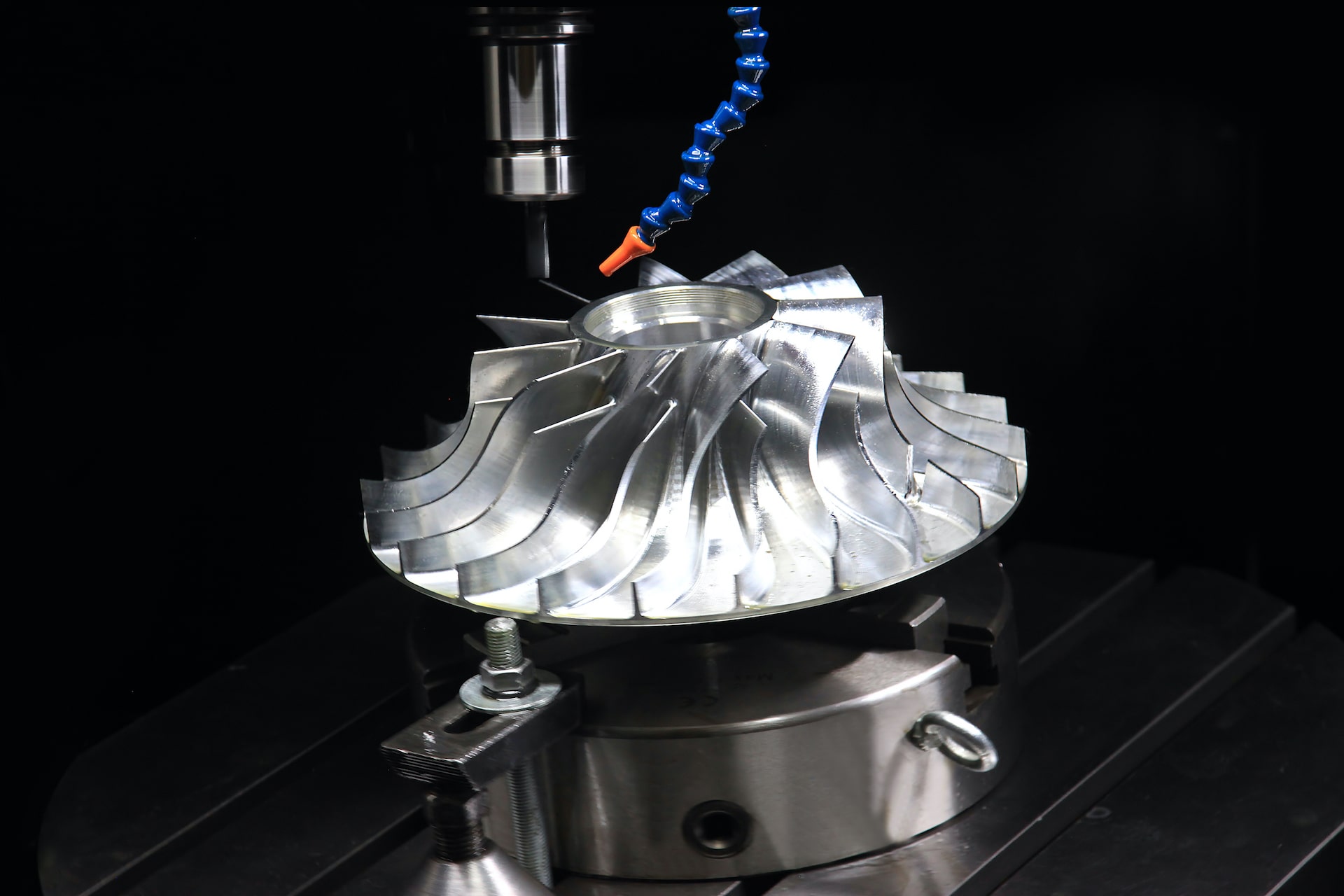