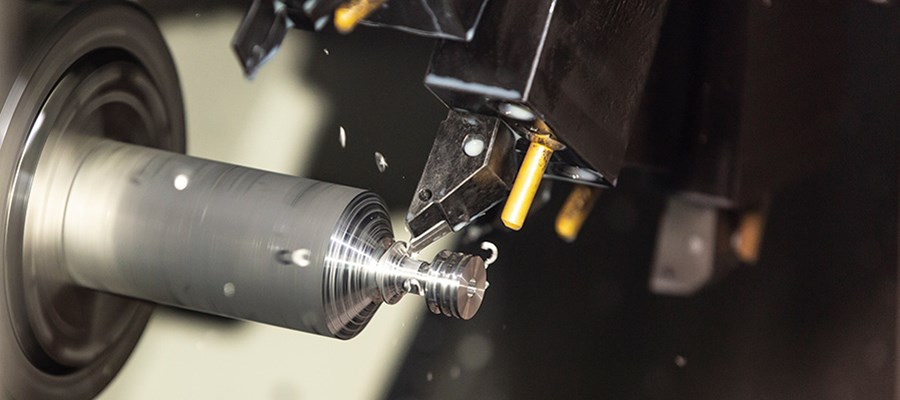
1. Turning
Turning of titanium alloy products is easy to obtain better surface roughness, and the work hardening is not serious, but the cutting temperature is high, and the tool wears quickly. In view of these characteristics, the following measures are mainly taken in terms of tools and cutting parameters:
Tool material: YG6, YG8, YG10HT are selected according to the existing conditions of the factory.
Tool geometry parameters: appropriate tool front and rear angles, tool tip rounding.
Low cutting speed, moderate feed rate, deep cutting depth, sufficient cooling, when turning the outer circle, the tool tip should not be higher than the center of the workpiece, otherwise it is easy to tie the tool. The angle should be large, generally 75-90 degrees.
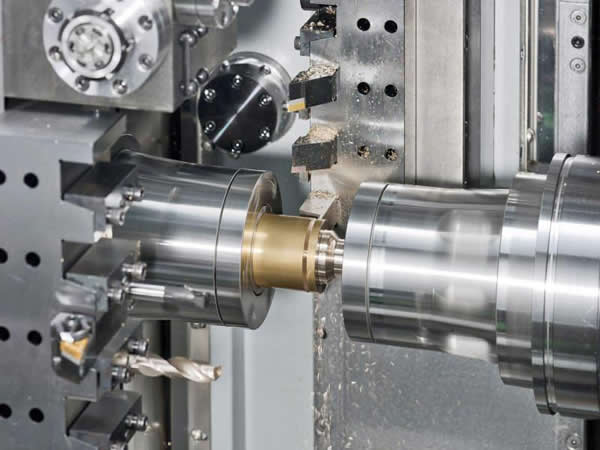
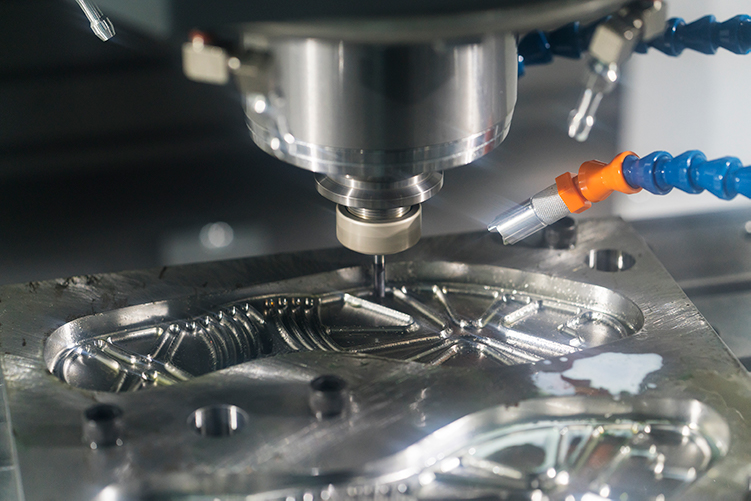
2. Milling
Milling of titanium alloy products is more difficult than turning, because milling is intermittent cutting, and the chips are easy to bond with the blade. Chipping, greatly reducing the durability of the tool.
Milling method: Climb milling is generally used.
Tool material: high speed steel M42.
Generally, the processing of alloy steel does not use climb milling. Due to the influence of the clearance between the screw and nut of the machine tool, when the milling cutter acts on the workpiece, the component force in the feeding direction is the same as the feeding direction, and it is easy to Make the workpiece table move intermittently, causing the knife to hit. For climb milling, the cutter teeth hit the hard skin when they start to cut in, causing the tool to break.
However, due to the thin to thick chips in up milling, the tool is prone to dry friction with the workpiece during the initial cut, which increases the sticking and chipping of the tool. In order to make the titanium alloy milling smoothly, it should also be noted that compared with the general standard milling cutter, the front angle should be reduced, and the rear angle should be increased. The milling speed should be low, and the sharp-toothed milling cutter should be used as much as possible, and the spade-toothed milling cutter should be avoided.
3. Tapping
In the tapping of titanium alloy products, because the chips are small, it is easy to bond with the cutting edge and the workpiece, resulting in a large surface roughness value and a large torque. Improper selection of taps and improper operation during tapping can easily lead to work hardening, extremely low processing efficiency and sometimes tap breakage.
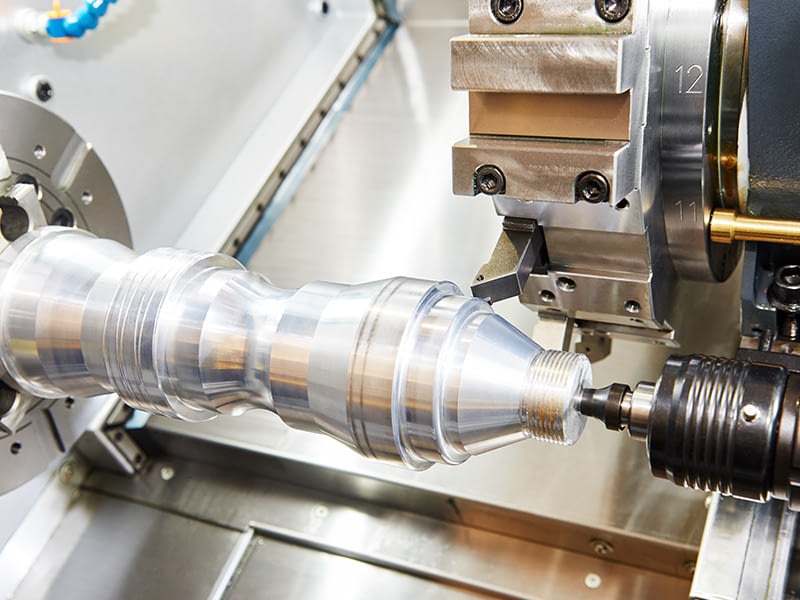
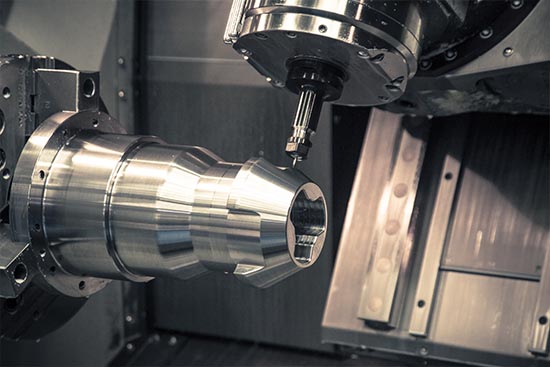
It is necessary to choose a thread of jumping teeth taps in place, and the number of teeth should be less than that of standard taps, generally 2 to 3 teeth. The cutting taper angle should be large, and the taper part is generally 3 to 4 thread lengths. In order to facilitate chip removal, a negative inclination angle can also be ground on the cutting cone. Try to use short taps to increase tap rigidity. The inverted taper part of the tap should be appropriately larger than the standard one to reduce the friction between the tap and the workpiece.
Post time: Mar-04-2022